Een spijkerbroek gaat door vele handen en is een van de ingewikkeldste kledingstukken om te verduurzamen. Jeansmerk Kuyichi die door Triodos gefinancierd wordt was het eerste Nederlandse merk dat werkte met 100 procent biologisch katoen. Ze geven ons inzicht in de hele keten en zo leer je stap voor stap wat er bij de productie van een spijkerbroek komt kijken.
Stap 1: Katoenplantage
Het begint allemaal bij de katoenboer. De katoenteelt is wereldwijd een grote werkgever: volgens het Wereld Natuur Fonds werken er 250 miljoen mensen in de katoenproductie, in ontwikkelingslanden is dat zelfs 7 procent van de bevolking. Maar het is geen makkelijk gewas: de katoenplant is bijzonder kwetsbaar voor insectenplagen en schimmels. Daarom worden er veel bestrijdingsmiddelen gebruikt – katoen heeft niet voor niets de bijnaam ‘the worlds dirtiest crop’. En dat heeft volgens Zoé Daemen, sustainabilitymanager bij Kuyichi, grote gevolgen. “In gebieden waar veel katoen wordt gekweekt, zie je dat mensen ziek worden, van oogproblemen tot kankers. Boeren beschermen zichzelf bijvoorbeeld niet goed genoeg bij het gebruik, maar de middelen spoelen ook uit en komen in het drinkwater terecht.”
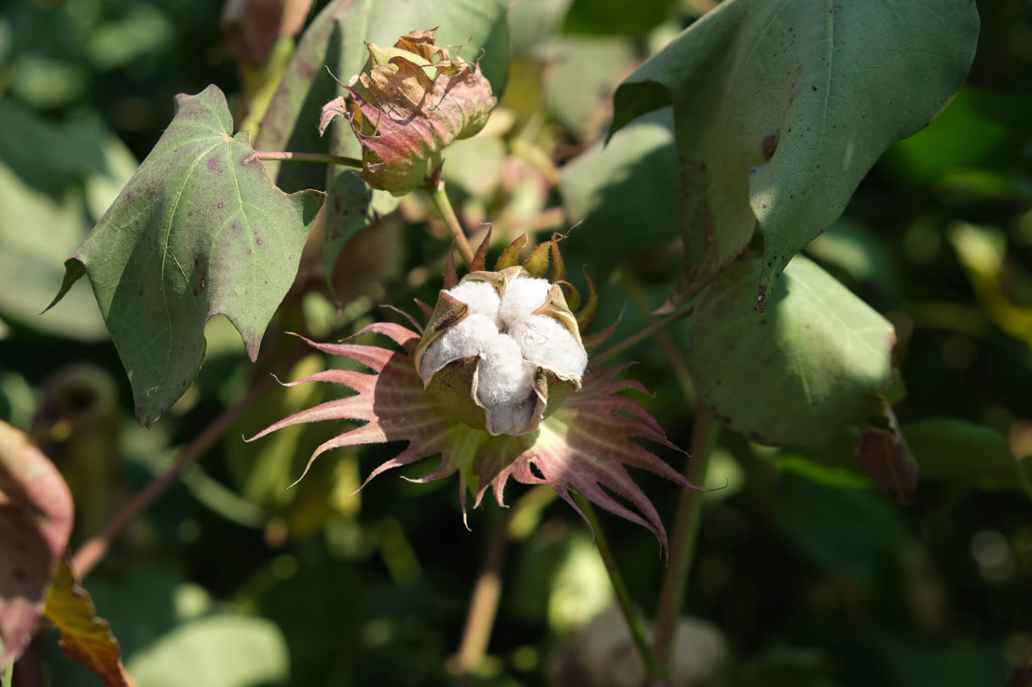
Nog niet 2 procent van de katoen die wereldwijd geproduceerd wordt is biologisch. “Wij nemen alleen biologische katoen af met het GOTS-keurmerk. Bij biologische katoenteelt is het uitgangspunt om vooral het bodemleven gezond te houden, en worden geen pesticiden en kunstmest gebruikt. Een gezonde bodem houdt bovendien meer water vast, waardoor je minder hoeft te beregenen.” Hoeveel water het kost om een kilo katoen te produceren verschilt heel erg per regio, zegt Daemen. De katoenteelt in het kurkdroge Uzbekistan, waarmee de Sovjet-Unie in de jaren zestig begon, is een van de grootste veroorzakers van het opdrogen van het Aralmeer, ooit het op 3 na grootste meer ter wereld.
Het probleem is dat het voor boeren lastig is om hun bedrijfsvoering biologisch te maken. Daemen: “De boeren moeten een proces door van gemiddelde 3 jaar en brengt veel kosten en onzekerheid met zich mee. Hun oogst kan in die jaren flink teruglopen omdat ze geen genetisch gemodificeerde zaden meer mogen gebruiken en geen bestrijdingsmiddelen. Tegelijkertijd mogen ze nog niet het label biologisch voeren dat ze verzekert van een hogere prijs. Wij helpen boeren met omschakelen naar biologisch door samen met onze denimproducent Bossa garant te staan voor het afnemen van hun oogst in de periode dat ze omschakelen.”
Stap 2: spinnen en verven
Van de geplukte katoen, die eerst nog bij een zogenoemde ‘ginner’, door een ontkorrelmachine gaat om de zaden eruit te halen, worden linten gemaakt, die tot draden worden gesponnen. Daemen: “Bij jeans worden de draden geverfd, dus niet de gewoven stof. De typische spijkerbroekenkleur wordt gemaakt met de kleurstof indigo, die niet tot het binnenste van de draad doordringt. Zo blijft een witte kern over. Hoe meer je van de draad afslijt bij het dragen, hoe lichter die op bepaalde plekken wordt.”
Maar indigo is geen efficiënte kleurstof. “Indigo moet oxideren om blauw te kleuren. Een witte stof wordt geel-groen als je die in het indigobad stopt. Onder invloed van zuurstof gaat de verf oxideren en ontstaat de blauwe kleur. De draad gaat door 2 tot 9 baden heen, om tussendoor aan de lucht te oxideren. Daarnaast hecht indigo zich niet zo goed, dus heb je stoffen nodig die dat bevorderen.” Het levert een afvalstroom op met chemische stoffen, die in gebieden waar jeans geproduceerd worden tot grote problemen leiden, inclusief blauwe rivieren met dode vissen.
“Onze producenten moeten om het label GOTS te mogen voeren goede filterinstallaties aanbrengen, om te voorkomen dat er gevaarlijke stoffen in de omgeving komen. Onze denimfabrieken zijn daarnaast ook lid of maken gebruik van ‘Zero Discharge of Hazardous Chemicals’ die de negatieve chemische impact van de industrie wil terugbrengen. Maar ook dan ontstaan er in het proces zoutkristallen die niet biologisch afbreekbaar zijn, voor die afvalstroom is nog geen nieuwe bestemming gevonden. Er is inmiddels ook indigo te verkrijgen zonder aniline, een bijzonder schadelijke stof. Daarnaast worden er door onze producenten ook nieuwe technieken ontwikkeld om het aantal kleurbaden te verminderen. We weten daarbij gelukkig dat het keurmerk GOTS op veel vlakken strenger is op schadelijke stoffen dan de EU-wetgeving.”
Stap 3: Weven
Van de draad wordt vervolgens in dezelfde fabriek een stof geweven met het kenmerkende schuine weefpatroon van de spijkerbroek. Daemen: “Hier wordt een groot deel van de kwaliteit van de stof bepaald: hoe dik en stevig maak je die, doe je er wel of geen stretch bij. Zwaardere stoffen gaan langer mee. Stretch wordt gecreëerd met kunststof elastaan, dat snel kan gaan lubberen. Daarnaast is een stof niet meer goed te recyclen als er te veel elastaan in zit. Wij gebruiken nooit meer dan 3 procent elastaan per broek, en wij gebruiken een elastaan die duurzamer is doordat die niet op spanning reageert, maar geactiveerd wordt door lichaamswarmte. We maken ook ‘rigid denim’, die is honderd procent katoen en steviger. Maar die moet je echt inlopen, voordat die zich vormt naar je lichaam. Ondertussen zijn veel consumenten niet meer bereid om een paar dagen te ploeteren in een strakke broek voordat die op de juiste plekken wat losser zit.”
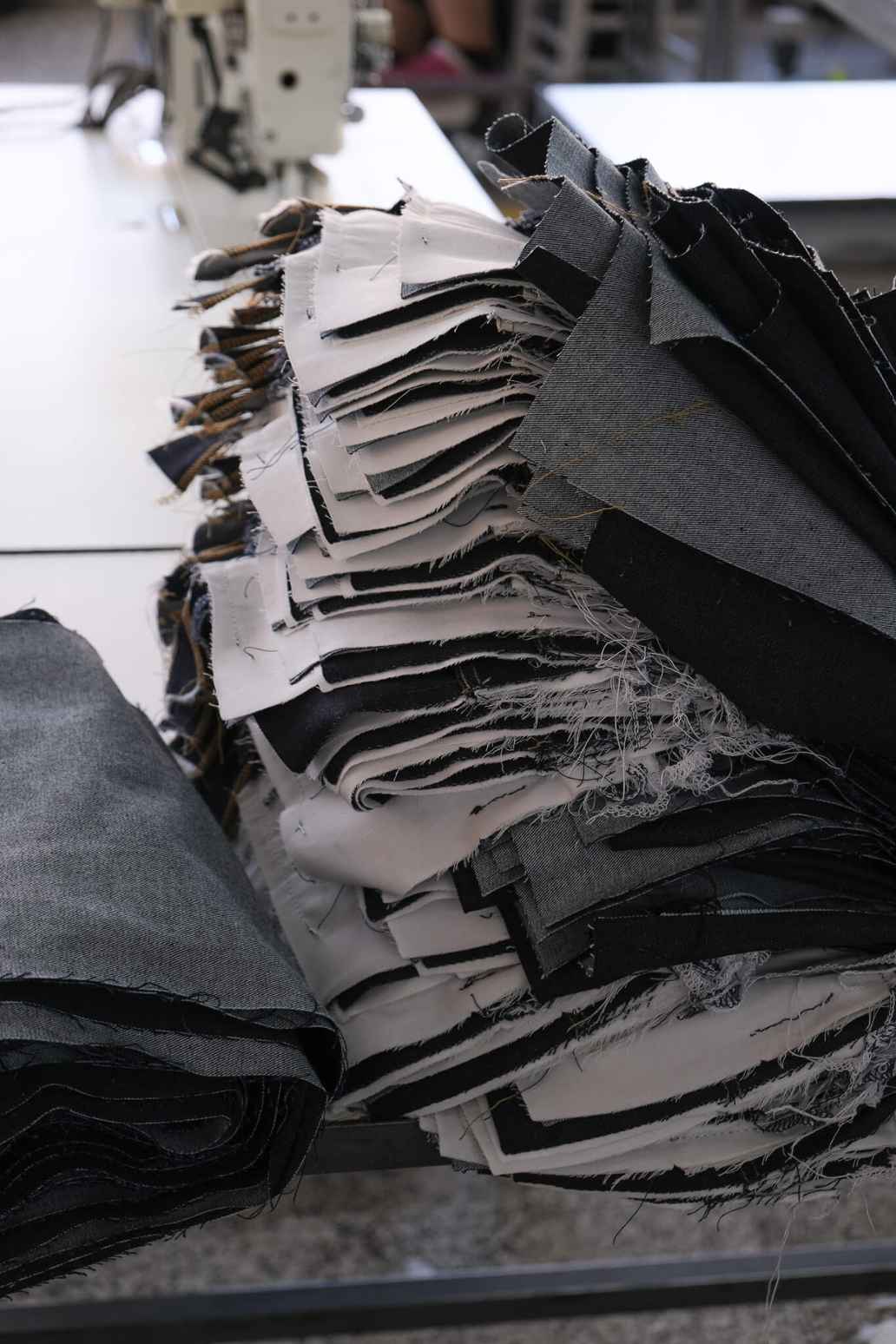
Stap 4: snijden en naaien
Het goede nieuws: in steeds meer fabrieken worden lasersnijders gebruikt om de patroonstukken te snijden. Daemen: “Het scheelt als dat geen mensenwerk meer is, want het is erg gevaarlijk. Als het snijden met de hand gebeurt dragen mensen maliënkolder-handschoenen om hun vingers te beschermen.” In de naaiateliers worden die stukken wel door mensen aan elkaar genaaid. “Iedereen in de fabriek heeft een taak en een gespecialiseerde naaimachine: een die een rits aanzet, een die de tailleband aan het been zet, een die de achterzak aannaait.” Omdat er in veel naaiateliers nog veel misgaat op het gebied van lage lonen, overwerken en veiligheid, is Kuyichi aangesloten bij de Fair Wear Foundation. “Die houden OESO-richtlijnen aan bij het doorlichten van onze keten: is er geen kinderarbeid, is de werkomgeving veilig? Zijn mensen vrij om hun contract op te zeggen? Uit die controles komen vaak wel wat dingen, die gaan we dan samen met de fabriek verbeteren. Tijdens de coronapandemie hebben we ervoor gezorgd dat medewerkers van onze leverancier in Turkije toch hun volledige loon kregen uitbetaald.”
Stap 5: het wassen
En dan is er nog een laatste, potentieel erg vervuilende stap. “Omdat mensen graag jeans dragen die al ‘versleten’ of vervaagd is, moet die in de zogenoemde ‘laundry’ laagjes van de vezels worden afgeschraapt zodat de wittere binnenkant van de draden zichtbaar wordt. Dat gebeurt doorgaans met heftige chemicaliën.” Ook hier is het zaak dat het afvalwater goed gefilterd wordt voor het in de omgeving komt. Kuyichi werkt met fabrieken die het gebruik van chemicaliën verminderen, bijvoorbeeld door bubbels of stoom te gebruiken in plaats van een wasmachine. De E-flow bubbelmachine voor het bleken en soepeler maken van stoffeen reduceert het watergebruik naar 1 glas per broek, gebruikt 90 procent minder chemische stoffen en 40 procent minder energie.” In 2021 kreeg meer dan 80 procent van de kleding van Kuyichi het groene ‘lage impact’-label van Jeanologica, een organisatie die een methodologie ontwikkelde om het water- energie- en chemicaliëngebruik van het wasproces te meten.
Ook hier zijn soms weer mensenhanden nodig: om met een schuurpapiertje slijtage aan te brengen. “Dat kan ondertussen ook met lasers, maar consumenten beseffen zich denk ik niet door hoeveel mensenhanden een broek gaat.” Een ‘dry jeans’ is niet door dit proces geweest. “Maar die is dus wel stijver en helemaal dezelfde kleur”.
Stap 6: in de winkel
Daemen: “Door de jaren heen slagen we er steeds beter in onze productie relatief dichtbij, in Turkijke, te organiseren. Hierdoor is de uitstoot van CO2 sterk verminderd. De rest compenseren we.”
Waar let je op als consument in de winkel?
Er zijn naast Kuyichi een aantal andere duurzame spijkerbroekenmerken die werken met gecertificeerde biologische katoen, gerecyclede katoen, fabrieken met goede werkomstandigheden en minder vervuilende was- en verfprocessen. Bijvoorbeeld Nudie Jeans, Kings of Indigo en Armedangels. Je kunt in de winkel letten op het Oeko-Tex-keurmerk (voor kwaliteit en een check op chemische stoffen), op GOTS (voor biologische katoen en ook een check op chemische stoffen) en het label van Fair Wear (voor onder andere arbeidsomstandigheden). Het label van RCS garandeert dat een broek meer dan 5 procent gerecycled materiaal bevat.
Stap 7: Recycling
Kledingafval maakt ongeveer 5 procent uit van de wereldwijde afvalbelt. Naar schatting wordt van minder dan 1 procent oude jeans weer nieuwe gemaakt. De techniek moet nog verbeteren, vertelt Daemen. “Gerecyclede vezels zijn korter en daardoor is de kwaliteit lager. Nu houden we 20 procent gerecyclede vezels aan als bovengrens per broek, maar er worden snel betere technieken ontwikkeld om dit percentage omhoog te krijgen. Daarnaast zijn er nu machines die polyester van katoen kan scheiden. Het gaat nu echt hard vooruit.” Het percentage gerecyclede vezels in de collectie van Kuyichi neemt elk jaar toe, in 2021 was dat 14, 5 procent.
Consumenten kunnen volgens haar erop letten dat ze spijkerbroeken niet in de afvalbak gooien, maar in de kledingbak. “Het lijkt erop dat we door de beelden van de enorme kledingberg ontmoedigd zijn geraakt, maar er zijn echt goede bedrijven die met die ingebrachte kleding aan de slag kunnen.” Sommige merken hebben een eigen inname-systeem. Daarmee is Kuyichi kortgeleden begonnen.
Bedankt voor je reactie!
Bevestig je reactie door op de link in je e-mail te klikken.